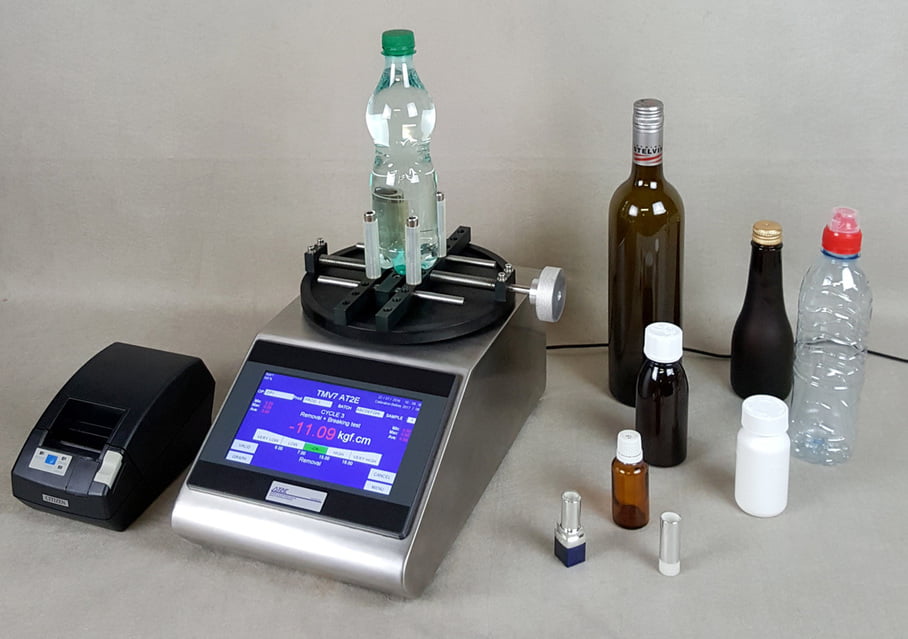
In today’s industrial landscape, ensuring product quality and safety is paramount, and the use of a bottle torque tester becomes indispensable to achieve these goals. These devices are designed to precisely measure the closure torque of bottle caps, ensuring they are adequately sealed to prevent leaks and maintain the integrity of the contents. Moreover, the accuracy provided by these testers helps maintain production consistency, a crucial factor for success in today’s competitive market.
Implementing a bottle torque tester in your production line not only elevates quality standards but also optimizes processes, reducing waste and operational costs. Choosing the right tester can be influenced by various factors, including the type of bottle, product specifications, and regulatory requirements. This article will explore how to select the appropriate equipment for your needs, discuss preventative maintenance, and highlight success stories that illustrate improvements achieved through effective torque tester implementation.
Introduction to Bottle Torque Testers
In the vast world of manufacturing and packaging, the role of a bottle torque tester is critical for ensuring product safety and consumer satisfaction. These devices are used to apply a specific torque to a bottle cap to determine its optimal tightness. The correct application of torque ensures that the contents are securely sealed to prevent spills or contamination. This is particularly important in industries such as pharmaceuticals and food and beverages where safety and hygiene are paramount. By ensuring that caps are neither too tight nor too loose, bottle torque testers help maintain the quality and integrity of the product throughout its shelf life.
The effectiveness of a bottle torque tester is evident in its ability to maintain consistent cap application across thousands of bottles. Companies rely on these testers to comply with strict industry regulations and to avoid the costly repercussions of product recalls or consumer complaints. As automation and precision become increasingly important in production lines, the demand for reliable bottle torque testers continues to grow. This tool not only helps in meeting quality standards but also plays a crucial role in enhancing production efficiency and reducing manual labor.
Choosing the Right Bottle Torque Tester
Selecting the appropriate bottle torque tester for your production line is crucial for maintaining high-quality standards. The first step is to understand the specific needs of your product and packaging. Different types of bottles and caps require different torque settings, which means the tester must be versatile enough to accommodate these variations. Additionally, the tester should be easy to integrate into existing production lines and simple for operators to use.
Durability is another key factor when choosing a bottle torque tester. Industrial environments can be harsh, and equipment needs to withstand the wear and tear of continuous use. Look for testers built with high-quality materials that offer long-term reliability. Moreover, modern testers come equipped with digital interfaces that provide real-time feedback and data analysis. This technology not only enhances the accuracy of torque application but also allows for better process control and troubleshooting.
Another important aspect is the tester’s ability to adapt to various bottle sizes and shapes. This flexibility ensures that the same device can be used across different lines and products, making it a cost-effective solution. Additionally, consider the speed of the tester—how quickly it can process bottles without compromising on accuracy. High-speed testers are essential for high-volume production environments where efficiency is key.
Finally, ensure that the torque tester you choose complies with all relevant safety and quality regulations. This compliance not only protects your products but also safeguards your company against legal issues. It’s wise to select a tester that comes with comprehensive support and service options. Having access to expert maintenance and repair services can significantly extend the life of your equipment and prevent downtime.
Key Benefits of Using a Bottle Torque Tester
The implementation of a bottle torque tester in a production line offers several substantial benefits that can transform manufacturing processes. One of the primary advantages is the assurance of consistent product quality. By standardizing the torque applied to each bottle cap, manufacturers can avoid issues related to under-tightening, such as leaks and contamination, or over-tightening, which can cause package damage or make opening difficult for consumers. This consistency is crucial for maintaining brand reputation and customer trust, especially in sectors like pharmaceuticals and food and beverage.
Moreover, bottle torque testers can significantly reduce the cost associated with product recalls and returns. Accurate torque application ensures that each bottle meets industry standards and consumer expectations, which decreases the likelihood of customer complaints and returns due to packaging failures. This precision also helps in complying with stringent regulatory requirements, preventing potential legal consequences and fines associated with non-compliance.
Integrating Bottle Torque Testers into Automated Systems
Integrating bottle torque testers into automated production lines can lead to enhanced efficiency and throughput. Automated systems equipped with torque testers do not just streamline the process but also improve the accuracy of cap application, minimizing human error. The integration allows for continuous operations, which can significantly increase production rates. This setup is ideal for industries requiring high-volume output with consistent quality.
Automation also provides the ability to monitor and adjust settings in real-time. If a bottle does not meet the specified torque value, the system can immediately flag it for review or reprocessing, thereby ensuring that no faulty product reaches the consumer. This level of control is crucial for maintaining stringent quality standards and operational efficiency.
The data collected by automated systems can be used for quality control and process optimization. By analyzing trends and identifying issues in real-time, manufacturers can make informed decisions about adjustments to the production process. This proactive approach to quality assurance not only reduces waste but also helps in pinpointing areas for improvement.
Additionally, automation reduces labor costs and the physical strain on workers. Automated bottle torque testers require minimal human intervention, which not only cuts down on labor costs but also reduces the risk of injuries associated with manual handling. This aspect is particularly important in maintaining a safe work environment and can also contribute to higher employee satisfaction and lower turnover rates.
Enhancing Product Safety with Accurate Torque Application
Using a bottle torque tester ensures that each product is sealed to exact specifications, which is paramount for product safety. Accurate torque application is crucial for preventing product tampering and ensuring that the seal is secure. This is especially important in industries where consumer safety is directly linked to product integrity, such as in pharmaceuticals and food products.
The precision of a torque tester helps in maintaining a hermetic seal, which protects the product from external contaminants and ensures its shelf life. This level of reliability is vital for products that are sensitive to environmental factors, such as moisture or air. Ensuring a perfect seal every time not only reduces the risk of contamination but also supports compliance with health and safety regulations.
Accurate torque testing also plays a critical role in sustainability efforts. By ensuring that caps are applied correctly, manufacturers can avoid overuse of materials and reduce waste. This precise application helps in promoting more sustainable packaging practices and supports the broader goals of environmental responsibility within the industry.
Cost Reduction and ROI from Bottle Torque Testers
Investing in a high-quality bottle torque tester can yield a significant return on investment by reducing operational costs and enhancing product quality. The upfront cost of purchasing and installing a torque tester is offset by the long-term savings from fewer product returns, less waste, and reduced risk of compliance issues. This cost-effectiveness is a crucial consideration for businesses looking to optimize their production lines.
By minimizing the need for manual re-checks and adjustments, bottle torque testers can also decrease downtime in production. This increase in efficiency allows for more products to be processed within the same time frame, boosting overall productivity. The reliability of automated torque application means less supervision is required, freeing up resources to be allocated elsewhere in the production process.
The long-term benefits also include fewer customer complaints and enhanced brand reputation. When consumers consistently receive products that meet high standards, it fosters loyalty and trust in the brand, which can lead to increased sales and market share. Moreover, companies that demonstrate a commitment to quality and safety through the use of advanced technology like bottle torque testers are often viewed more favorably by consumers and regulators alike.