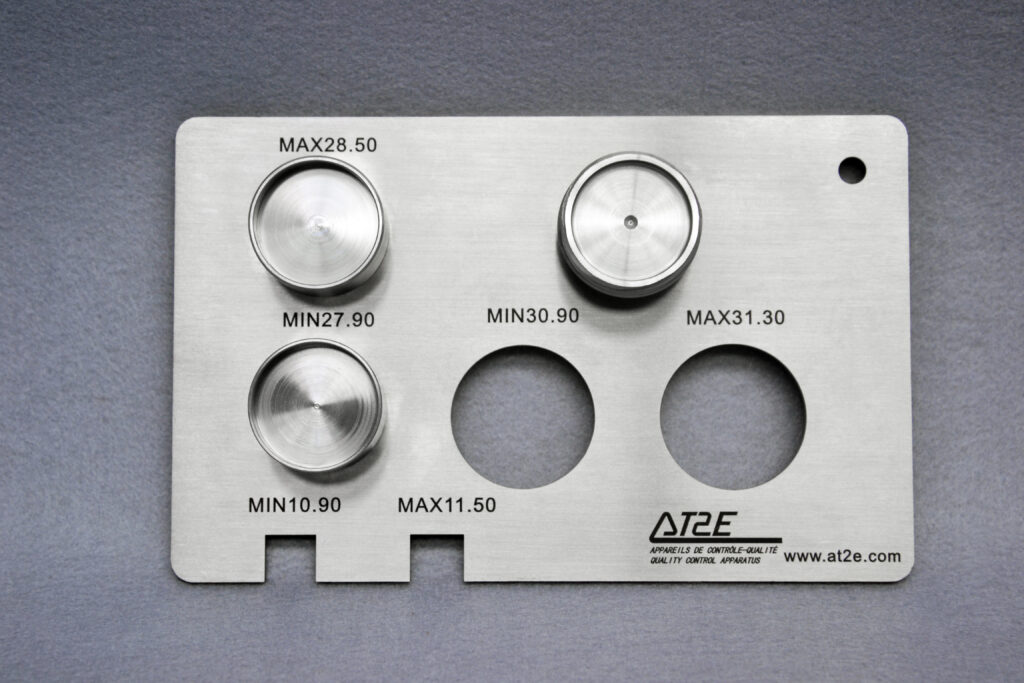
Introduction
Packaging quality is a critical aspect of product delivery, affecting both the safety and satisfaction of consumers. To maintain high standards, manufacturers use various tools, one of which is the Go-no-Go gauge. This precision instrument ensures that packaging components meet specific dimensional criteria, preventing defects and ensuring consistency.
What is a Go-no-Go Gauge?
A Go-no-Go gauge is a simple yet effective inspection tool used to check whether a part’s dimension falls within specified limits. It consists of two tests: the “Go” test, which verifies if the part meets the minimum acceptable dimensions, and the “No-Go” test, which ensures the part does not exceed the maximum dimensions.
Importance of Go-no-Go Gauges in Packaging
- Consistency: Ensures that every packaging component meets quality standards.
- Efficiency: Quick and easy to use, reducing inspection time.
- Cost-Effective: Minimizes the need for expensive measurement tools and reduces waste from defective parts.
- Compliance: Helps in meeting industry standards and regulations.
How Go-no-Go Gauges Work
The gauge has two ends: the “Go” end, which should fit into or over the part being tested, and the “No-Go” end, which should not fit. This binary result simplifies the inspection process, making it accessible even to non-technical staff.
Applications in Packaging
Go-no-Go gauges are used in various packaging applications:
- Bottle Caps: Ensuring that caps fit securely without leaks.
- Containers: Verifying that containers meet volume and dimensional specifications.
- Seals and Closures: Checking the integrity and proper sealing of packaging.
Conclusion
The Go-no-Go gauge is an invaluable tool in the packaging industry, ensuring that all components meet stringent quality standards. Its simplicity, efficiency, and reliability make it a preferred choice for quality assurance professionals.