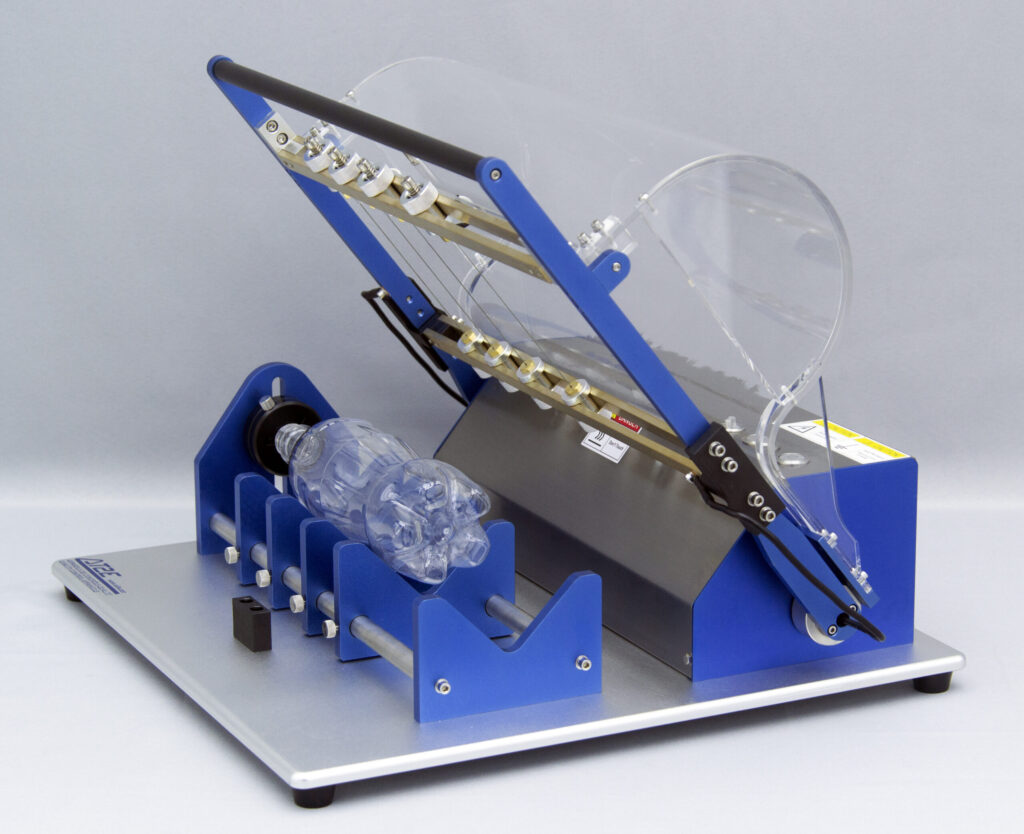
Introduction
In the world of manufacturing, particularly in the production of PET (polyethylene terephthalate) bottles, quality control is paramount. Accurate sectioning plays a crucial role in ensuring the integrity, safety, and functionality of PET bottles. This blog post delves into the importance of precise sectioning in PET bottle quality control, highlighting key benefits, methods, and industry standards.
Table of Contents
- What is PET Bottle Sectioning?
- The Role of Accurate Sectioning in Quality Control
- Benefits of Accurate Sectioning
- Methods for Sectioning PET Bottles
- Industry Standards and Best Practices
- Conclusion
1. What is PET Bottle Sectioning?
PET bottle sectioning refers to the process of cutting and examining different sections of a PET bottle to evaluate its structural integrity, material distribution, and overall quality. This process is vital for identifying defects, inconsistencies, and areas that need improvement during the manufacturing process.
2. The Role of Accurate Sectioning in Quality Control
Accurate sectioning is essential for several reasons:
- Detection of Defects: By examining various sections of the bottle, manufacturers can detect defects such as wall thinning, stress points, and material distribution issues.
- Ensuring Uniformity: Consistent sectioning helps ensure uniform thickness and strength throughout the bottle, which is crucial for maintaining product safety and performance.
- Compliance with Standards: Precise sectioning ensures that PET bottles meet industry standards and regulations, avoiding potential legal and financial repercussions.
3. Benefits of Accurate Sectioning
- Enhanced Product Safety: Accurate sectioning helps identify weak points that could lead to bottle failure, ensuring that only safe products reach the market.
- Improved Quality Assurance: By maintaining high standards through precise sectioning, manufacturers can guarantee better quality products, leading to increased customer satisfaction.
- Cost Efficiency: Detecting and addressing defects early in the production process can save costs associated with recalls, returns, and waste.
- Competitive Advantage: Consistently high-quality products enhance brand reputation and provide a competitive edge in the market.
4. Methods for Sectioning PET Bottles
Several methods are employed for sectioning PET bottles accurately:
- Mechanical Cutting: Using specialized cutting tools to slice through the bottle at specific points.
- Laser Cutting: Utilizing precision lasers for clean and accurate cuts.
- Cryogenic Sectioning: Freezing the bottle and then cutting it to prevent deformation and achieve precise sections.
Each method has its advantages and is chosen based on the specific requirements of the quality control process.
5. Industry Standards and Best Practices
To maintain high-quality control standards, manufacturers follow several industry guidelines and best practices:
- ASTM Standards: Adhering to the American Society for Testing and Materials (ASTM) standards for PET bottle testing and sectioning.
- ISO Standards: Implementing International Organization for Standardization (ISO) guidelines for consistency and quality assurance.
- Regular Training: Ensuring that quality control personnel are regularly trained and updated on the latest sectioning techniques and standards.
6. Conclusion
Accurate sectioning in PET bottle quality control is indispensable for ensuring the safety, quality, and reliability of the products. By employing precise sectioning methods and adhering to industry standards, manufacturers can detect defects early, ensure uniformity, and maintain compliance, ultimately enhancing their brand reputation and customer satisfaction. Investing in accurate sectioning processes not only improves product quality but also provides significant cost benefits and a competitive edge in the market.